Custom Logo Mailing Corrugated Boxes Shipping Mailer Box
Corrugated boxes, with their vibrant printing colors, excellent protective functions, environmentally friendly low-carbon advantages, and easy processing characteristics, play an extremely important role in the circulation of goods. Their share in the entire packaging industry has been increasing. With brand owners’ increasing demands for exquisite printing on product packaging, the water-based ink printing technology for corrugated boxes faces more and more challenges. This article shares my insights on how to improve the quality of water-based ink printing by using improved equipment.
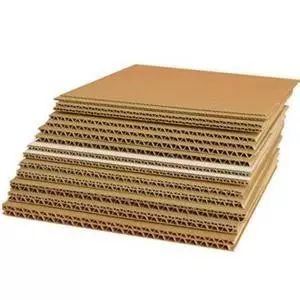
Handling White Spots in Printing
White spots in printing are the most common and challenging quality issue in corrugated box production. They occur due to poor ink absorption of the paper, dirty printing plates, or paper debris and dust on the cardboard. Traditional methods to address these issues include manual adjustments to the boxes and increasing the frequency of manual plate wiping.
While these methods have some impact, the improvement after adjusting the boxes is limited. Moreover, they lead to decreased efficiency, and excessive plate wiping results in water, electricity, and labor wastage.
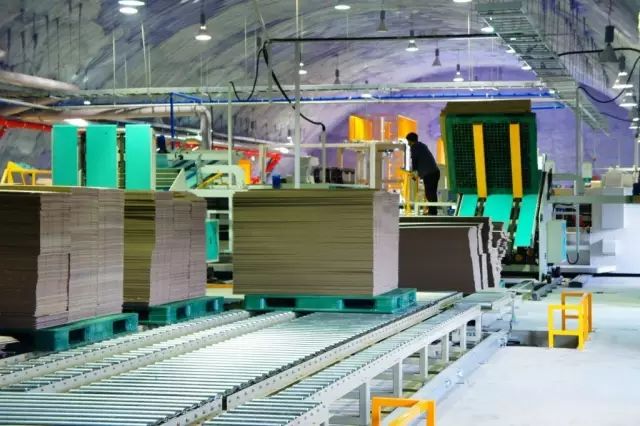
Through long-term observation and analysis during equipment installation, maintenance, and management, engineers found that the key factor causing white spots in printing is dust. The main source of dust is generated during single-knife sheeting. Based on this situation, two years ago, engineers installed electrostatic dust removal devices at the back end of the computer cross-cutting machine in the cardboard production line and the paper feeding section of the printing machine.
A blower is used in front of the computer cross-cutting machine to blow away or remove the paper debris hidden in the grooves during single-sheet cutting. Later, an electrostatic dust removal device is used at the paper receiving rack behind the computer cross-cutting machine to suck away the paper debris. In the gap between the paper feeding rubber ring and the paper feeding wheel of the printing machine’s paper feeding section, an electrostatic dust removal device is used to remove the dust on the cardboard, keeping the printing surface clean and dust-free. This ensures smooth ink application and uniform ink absorption when the product enters the ink rollers.
After these improvements, the printing results are significantly enhanced, fundamentally preventing the occurrence of white spots caused by dust during printing.
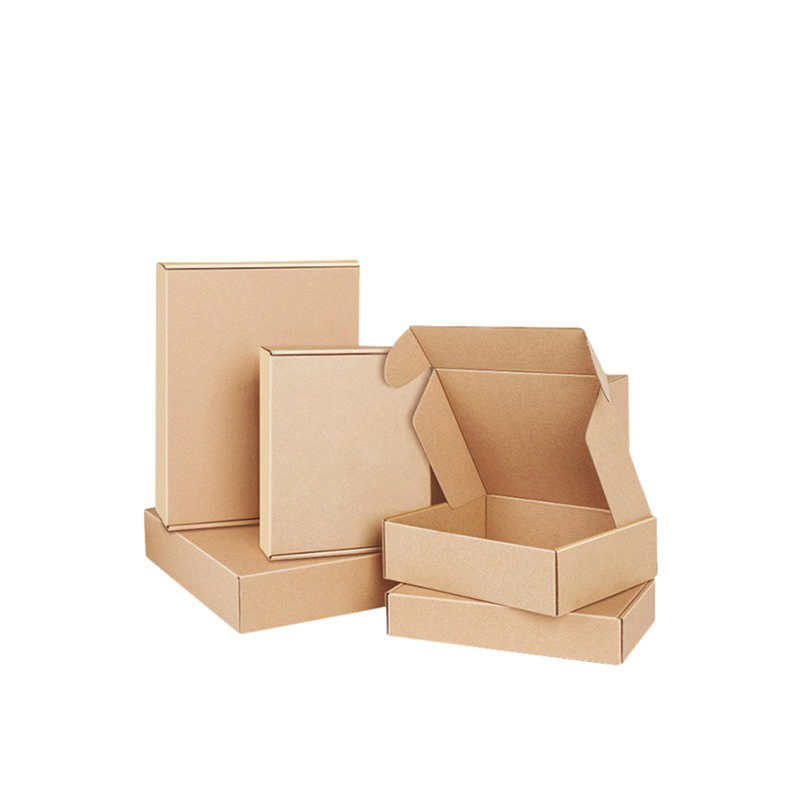
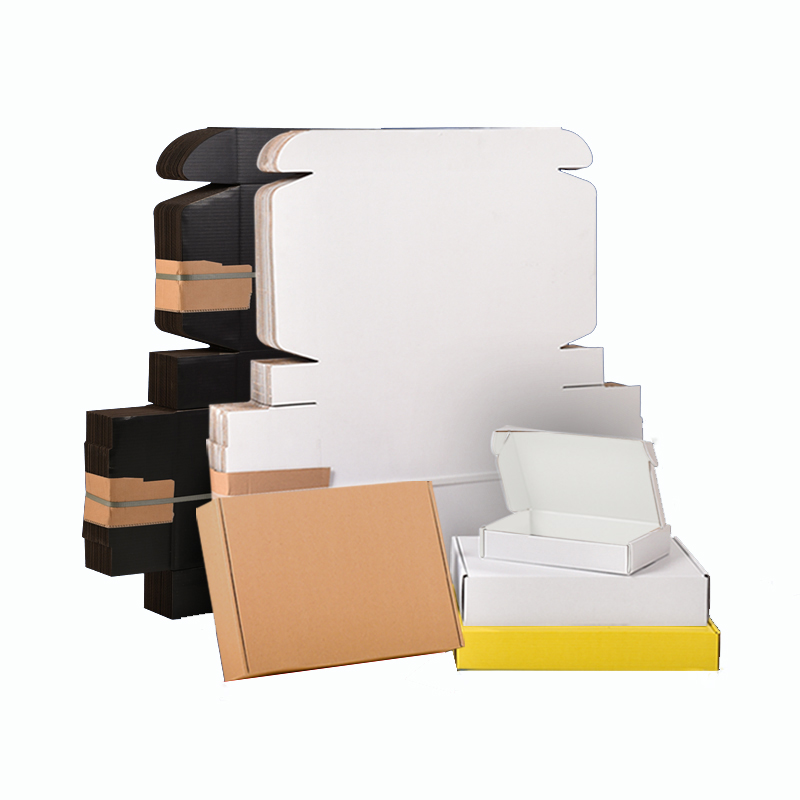
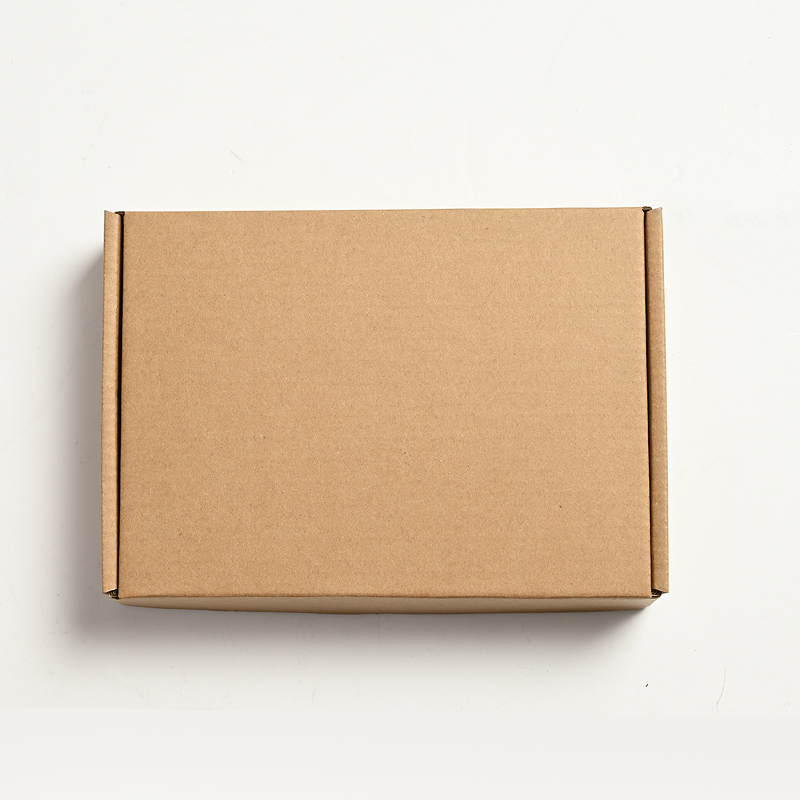