Custom Logo Mailing Corrugated Boxes Shipping Mailer Box
Handling Misalignment in Overprinting
Nowadays, product packaging increasingly emphasizes the artistic and three-dimensional aspects of patterns, allowing consumers to perceive the perfection of the purchased items from the external packaging. To achieve this goal, packaging printing must employ multicolor printing, specifically overprinting.
In the overprinting process, misalignment can occur when the colors from subsequent printing layers do not align accurately with the preceding layers, causing the printed pattern to deviate from the intended design and damaging the product’s image.
To address this specific issue, engineers conducted in-depth on-site investigations and research. Detailed calculations were made, ranging from the electronic control response speed to mechanical tolerance accuracy. Multiple improvements were implemented on existing equipment, and relevant equipment maintenance measures were formulated.
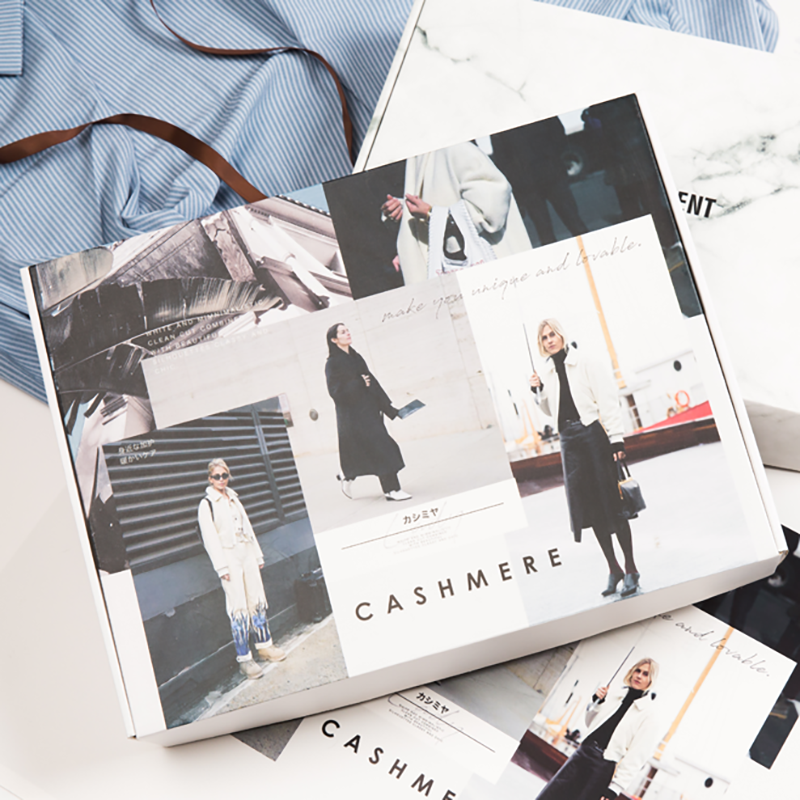
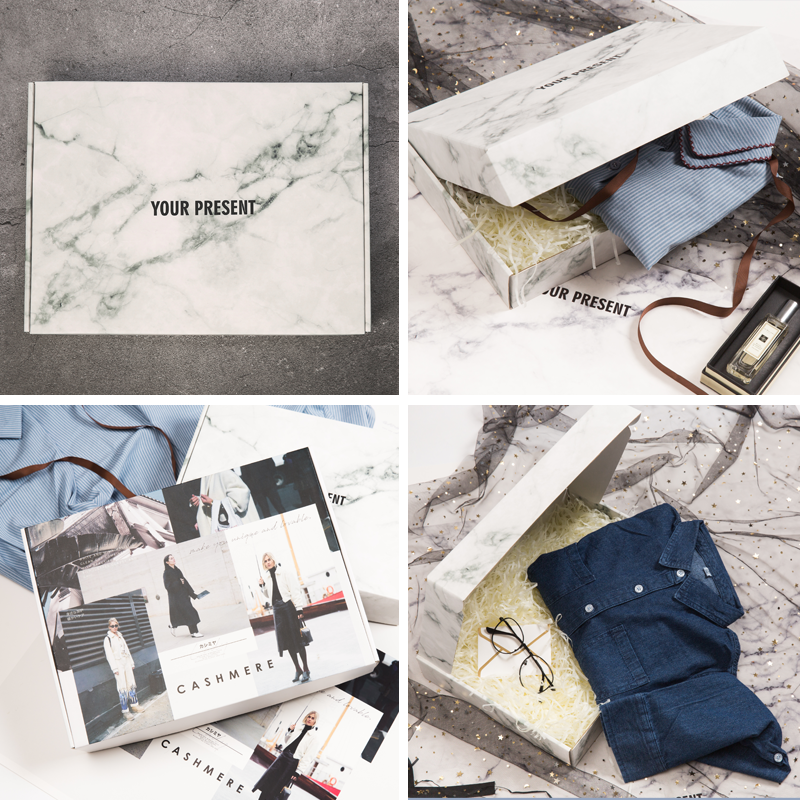
- Improving the Precision of Plate Cylinder Phase Positioning: The phase positioning of the plate cylinder is controlled using an encoder and counter. If the accuracy of the counter is too low, it results in inaccurate encoder positioning, leading to misalignment during printing. Typically, the counter response speed is 3K, but it often generates an error of ±1mm during positioning. After consulting with a control company in Taiwan, a 5K counter was produced, reducing the positioning error to 0.4mm.
- Timing Lubrication and Inspection of Transmission Mechanisms: During the paper feeding process, if the transmission mechanisms do not operate smoothly and steadily, each position where the cardboard arrives will vary, causing misalignment in overprinting. Therefore, correct maintenance and inspection of the equipment are crucial.Engineers developed a daily pre-operation checklist, which includes lubrication and maintenance tasks. Limits were set for the wear and tear of paper feeding wheels and circles; when they failed to meet the standards, they had to be re-ground, re-coated, or replaced, overcoming misalignment and skewing issues during the cardboard’s movement.
- Adopting Vacuum Paper Feeding: Traditional printing machines use top printing, relying on paper feed wheels to transfer cardboard. However, modern printing machines use advanced technology with bottom printing and top vacuum paper feeding. Vacuum paper feeding utilizes airflow to adhere the cardboard to the transfer wheel uniformly. It prevents misalignment and skewing, flattens bent cardboard, ensures accurate alignment during printing, and achieves more uniform ink distribution.
By implementing these improvements, misalignment issues in overprinting were effectively resolved, ensuring accurate and high-quality printing results.
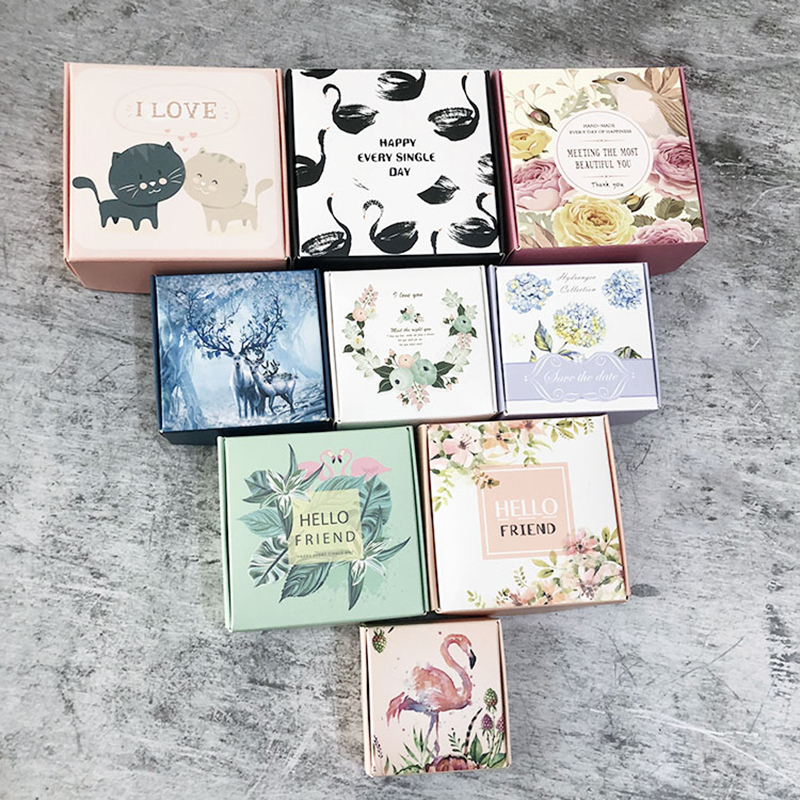
Handling Poor Ink Application in Printing
Poor ink application can be caused by paper quality issues, plate problems, and technical issues related to the inking rollers on the printing equipment. In high-standard corrugated box printing, mesh rollers are commonly used. For printing above 250 lines, these mesh rollers often face issues like ink residues clogging the mesh holes, leading to uneven ink application, insufficient ink quantity, and light ink issues.
Traditional methods, such as cleaning with water, non-water wiping, or using cleaning agents, have proven less effective. With these methods, a new inking roller’s lifespan can be less than a month, showing worse results than before.
The following methods effectively address the problem of poor ink application in printing:
- Install a Filter Screen in the Ink Bucket: Install a filter screen inside the ink bucket to prevent ink particles from entering the inking rollers.
- Regular Deep Cleaning with Mesh Roller Cleaner: Periodically (usually every two weeks), use a deep cleaning solution specifically designed for mesh rollers to clean them thoroughly.
- Daily Cleaning and Inspection: At the end of each working day, circulate water through the inking rollers. Use a magnifying glass with 60x to 100x magnification to inspect the mesh holes of the inking rollers. There should be no ink residues left in the holes. If any residues are found, immediately clean them with the deep cleaning solution.
By following these maintenance practices, the ink application on the inking rollers can be consistently kept in good condition.
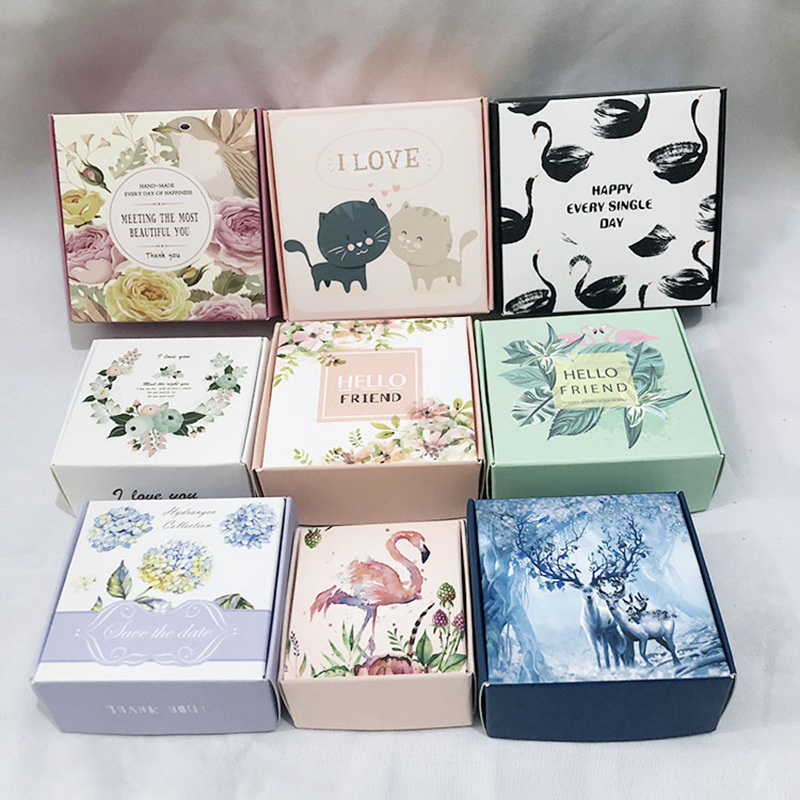